What is a plant shutdown?
A plant shutdown refers to the process in which all or part of the production in an industrial facility or factory is temporarily halted to perform maintenance, repairs, inspections, adjustments, or upgrades to equipment, machinery, systems, or facilities. These shutdowns are scheduled and planned in advance to minimize production interruptions and ensure safe and efficient plant operation.
Plant shutdowns can vary in duration, ranging from a few hours to several days or even weeks, depending on the nature of the required activities. During a plant shutdown, technical and maintenance personnel perform tasks such as equipment inspection and repair, replacement of worn parts, pipe and system inspections, software updates, and other procedures necessary to maintain the plant’s operation in optimal condition. Additionally, these shutdowns provide opportunities to implement technological improvements and optimize production processes.
The presence of contractors in plant shutdowns.
Plant shutdowns often require specialized external maintenance and technical companies, which provide a substantial number of qualified personnel, tools, and specific means to carry out the necessary tasks. Contractors are external workers who participate in the plant shutdown.
Contractors are accustomed to working on technical and maintenance tasks, but since they are not permanent plant workers, they may not be familiar with the specific risks of the particular plant. One of the main safety challenges during plant shutdowns is the contractors’ lack of familiarity with the site, as these operations typically occur in the same plant every 4 or 5 years, and personnel can change.
Moreover, a serious accident could lead to delays in the planned shutdown, resulting in direct economic impacts by postponing the resumption of production. In fact, according to a report from the American Petroleum Institute, 80% of these operations end up exceeding the projected costs if not adequately prepared and planned.
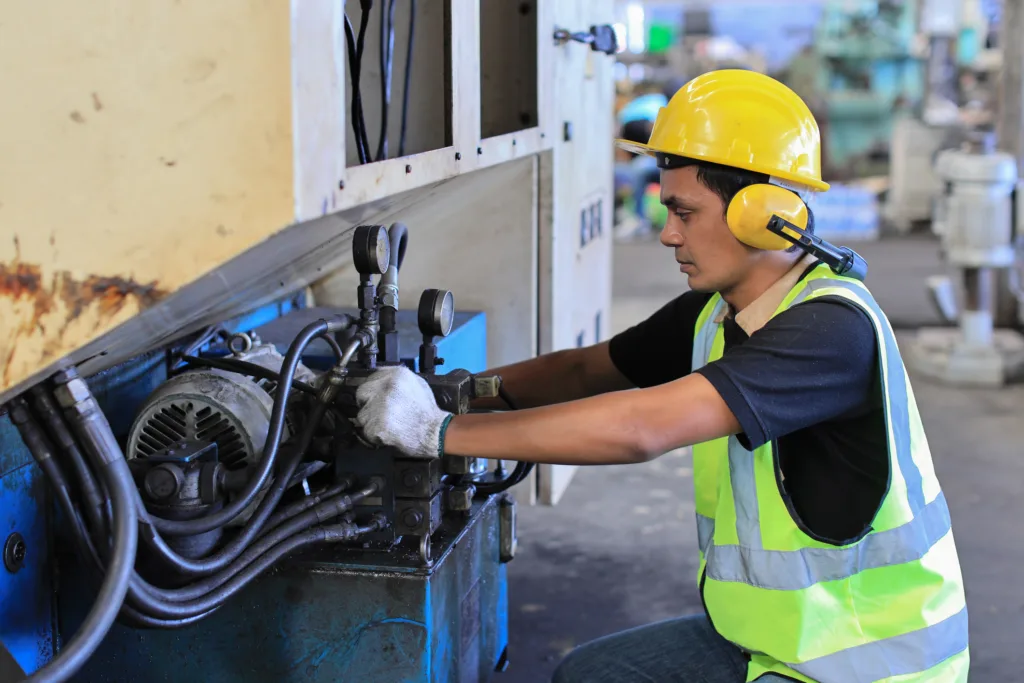
Common hazards in plant shutdowns.
Various factors can lead to various issues, with the most common being:
1# Lack of Planning: Attempting to carry out a large number of interventions in a short period of time without proper prior organization. Effective planning and experience are crucial for reducing downtime.
2# Inexperienced Contractors: It is vital to carefully select the contracted companies for the plant shutdown, ensuring that they can provide the required qualified personnel.
3# Increased Accidents: The probability of occupational accidents significantly increases with the presence of external personnel and maintenance work, necessitating additional efforts from HSE leaders to ensure the protection of all workers. This involves verifying the required training for the involved personnel, analyzing potential risks during the work execution, and evaluating the condition of the equipment and tools to be used.
Available technology for enhanced safety.
In addition to the standard personal protective equipment for workers, various technologies and practices can be used to enhance safety in plant shutdowns. These include:
- Control and Automation Systems: Process automation and advanced control systems allow more efficient and secure monitoring and control of operations during a plant shutdown. This includes precise equipment stopping and restarting, continuous monitoring of critical variables, and real-time adjustments.
- Fault Detection and Alarm Systems: Early warning systems and fault detection alert personnel to potentially dangerous situations. This involves continuous monitoring of sensors and devices to detect anomalies.
- Real-Time Location Systems: These systems enable the real-time tracking of workers and equipment, particularly useful for ensuring safety and coordinating activities during the shutdown.
- Robotics and Drones: Robots and drones can be deployed to inspect hard-to-reach or hazardous areas without exposing workers to unnecessary risks.
- Data Management and Analytics: Real-time data analysis and historical data storage can help identify patterns and trends that can improve safety and operational efficiency during a plant shutdown.
- Digital PPE: The use of digital personal protective equipment, such as the Drixit Tag, provides a wide range of solutions specifically designed for industrial workers, including panic buttons, detection of entry and presence in hazardous areas, height work detection, precise location in emergencies, and evacuation, among others. Its implementation helps prevent and mitigate industrial accidents, ensuring a successful plant shutdown and avoiding potential delays.
The combination of these technologies, along with proper training and a strong safety culture, contributes to achieving greater safety in plant shutdowns, minimizing risks for workers and ensuring an efficient return to normal operation.