There are historical preventive measures created to protect isolated workers. However, the inherent risk of their work situation makes it necessary to incorporate technology in order to effectively enhance their safety.
In several industries, especially those classified as “heavy industry”, there are workers who perform their tasks in isolation. Some of them work night shifts, others perform maintenance tasks, and there are those who operate in remote areas, among others. This type of work has its intrinsic risks, and therefore involves extraordinary safety measures. So what is the best way to protect isolated workers?
What is the definition of isolated workers.
Isolated workers are those who, regardless of the task they perform, work in environments where no other workers are present. According to the Technical Note on Prevention (NTP-344), a brief document that deals with a specific preventive issue, lone working means any activity that is carried out without being able to establish visual or auditory contact with other people, unless mechanisms such as telephones or radios are used.
In addition, a lone worker is considered to be a lone worker when he/she fulfills precisely this condition of isolation regardless of the time the task lasts: it can be from a whole shift to jobs lasting only one hour- In general, all industrial-type companies have lone workers, especially considering the people who perform safety and maintenance tasks. They tend to be in construction, utilities, oil and gas, agriculture and so on.
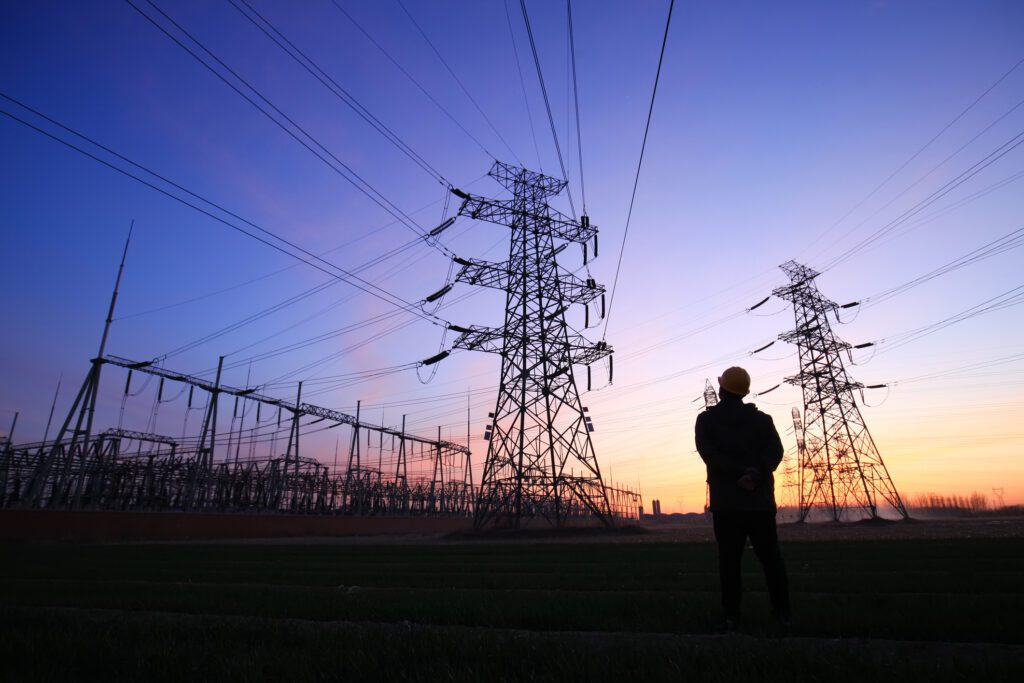
What are the risk factors to which they are exposed?
According to the Technical Prevention Note mentioned above, the risks to which isolated workers are exposed can be divided into two categories:
Safety risks
Within the safety risks, we have both accidents and lack of help after a critical situation. Accidents can be caused by machine failure as well as by human error or uncertainty. The latter tend to happen more easily in the case of isolated workers, since they do not have the supervision or accompaniment of another person who can correct the error.
On the other hand, safety risks include the lack of assistance after a critical situation: when an accident occurs, immediate action is essential and is not 100% guaranteed in the case of lone workers. This lack of immediate assistance can considerably aggravate the consequences of an accident.
Psychosocial risks
Psychosocial risks derive from the isolation itself, which can lead to altered behavior. Routine work and the absence of other people leads to a decrease in vigilance and may even alter the perception of time. Lack of information or the means to make decisions as a team can lead to inappropriate reactions, especially in unforeseen situations.
Moreover, isolation can lead to physical, intellectual or mental fatigue, generating stressful situations that increase the probability of accidents due to human error.
What are today’s safety protocols like?
Over the years, industrial companies created protocols to protect industrial workers. A very common one was to require communication between operator and supervisor every one to two hours. OSHA (Occupational Safety and Health Administration) guidelines on lone working state that employers should follow up throughout each shift “at regular intervals appropriate to the work task, to ensure their health and safety, and at the end of the task or at the end of the work shift, whichever comes first”.
This measure, which was necessary in the face of a lack of better tools, raises certain problems. First, it generates a constant discontinuity in work, affecting productivity and concentration, which can even be counterproductive. Another fundamental problem is that there are situations that require immediate response. In the event of an accident, an hour’s delay (or more, until it is established that the worker is definitely not coming into contact) can be fatal.
Other measures considered indispensable in the care of isolated workers are:
- Periodically assess potential hazards and high-risk situations.
- Develop clear and concise policies for lone workers.
- Train lone workers on best safety practices.
- Facilitate communication.
- Utilize the assistance of technology.
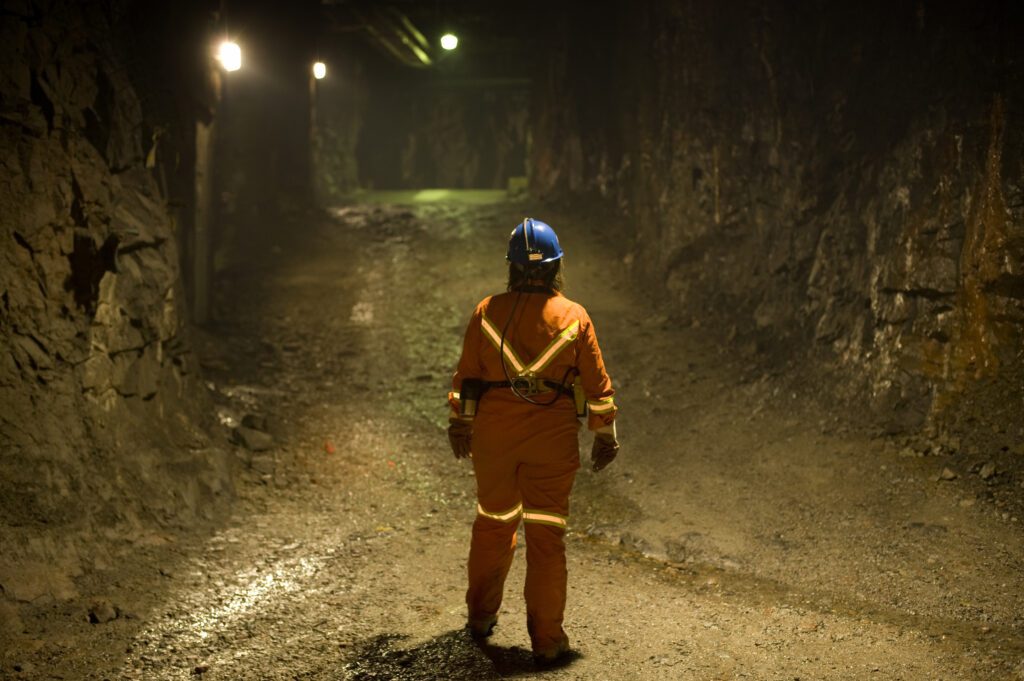
How to protect isolated workers with technology.
Considering the safety risks and psychosocial risks discussed above, it is interesting to analyze how the use of technology can help to improve both.
In the case of safety risks, there are devices that can immediately detect and report falls and hard knocks. The Drixit Tag, for instance, not only identifies these situations and notifies the supervisor, but also has a panic button that can be activated in emergency situations. Among other functionalities, it can be configured to identify if a person is detained for a long time (as in the case of cardiac arrest or fainting) or if he/she remains longer than necessary in areas that are hazardous to his/her health. It can also activate geolocation in cases of evacuation or emergencies, quickly locating the person in order to provide immediate assistance.
Psychosocial risks are also mitigated when workers have this type of devices that increase their protection. Knowing that they are protected and protected increases confidence, reduces stress levels and allows workers to concentrate on what is important: their work.