Safety events have consequences for the worker, whether injuries, fatalities, as well as consequences for the company, such as property damage and disruptions in operation, image, and costs.
The industry, has a significant share of these events, and some numbers give the magnitude: the International Energy Agency indicates that accidents in the sector represented 11% of fatal accidents in the world in 2018, in the same year estimated that the number of deaths was about 12,000. In Brazil, ABEEólica in 2019 recorded four fatal accidents during operation and maintenance of turbines and in 2020, ANEEL recorded 311 serious accidents, with 105 deaths, 30% more than the previous year. According to CUT from 2012 to 2022, there were 6.7 million accidents with 25,500 deaths, 15% due to operation of machinery and equipment.
The investigations indicate factors that contribute to accidents: lack of proper maintenance or problems in machines and equipment or tools causing cuts, crushes, and falls; inadequate environment with lack of lighting, ventilation, adequate space, or limited access; inadequate training regarding safety standards and procedures, leading to lack of knowledge of the risks of the activities and mistakes; excessive work hours, repetitiveness, and lack of adequate breaks leading to fatigue and stress, affecting concentration; mistakes or reckless attitudes, unsafe behavior such as running, jumping, and playing; and finally, inadequate use of personal protective equipment (PPE). e. running, jumping, and playing; and finally, inadequate use of personal protective equipment (PPE).
Therefore, adopting measures to prevent and eliminate risks, such as work safety programs, regular training, preventive maintenance of equipment and machinery, provision and control of PPE, and the use of technology, will create a safer environment.
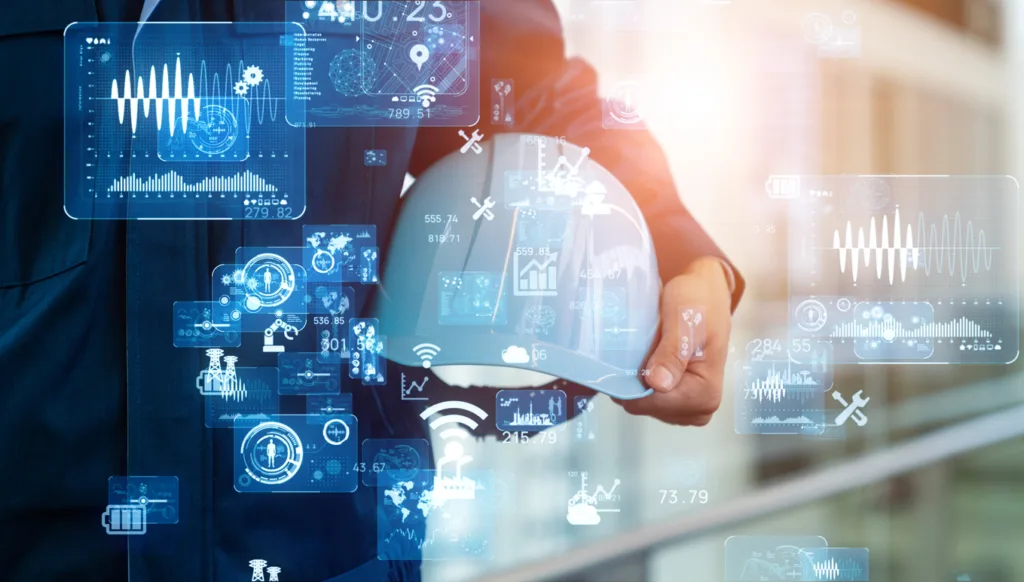
The Four Safety Truths
Back in 2014, the University of Colorado published a study called “The Four Safety Truths,” where they concluded:
- Safety inspections are essential to identify hazards and risks in the work environment, and should be complemented with training, proper equipment, and safe procedures.
- Reporting safety events identifies problems and prevents accidents, but the culture must create an environment where workers feel comfortable reporting problems and where management is proactive in resolving them.
- Safety is everyone’s responsibility, not just the responsibility of front-line workers; management has a key role in creating a culture and promoting actions for prevention.
- Safety is a continuous improvement process, so work proactively to prevent accidents and constantly evaluate safety processes and make adjustments whenever necessary, including technological innovation.I highlight the role of management, through “Safety Walk & Talk”, which focuses on safety issues, where they visit areas to talk to workers about safety and check safety measures by identifying potential problems and their solutions, which allows direct communication to solve problems and speeds up decision making on possible solutions and investments in technology.
I highlight the role of management, through “Safety Walk & Talk”, which focuses on safety issues, where they visit areas to talk to workers about safety and check safety measures by identifying potential problems and their solutions, which allows direct communication to solve problems and speeds up decision making on possible solutions and investments in technology.
Predictive” approaches to occupational safety and their application in industry.
This is part of a “predictive” approach, combining with technologies such as data analytics, machine learning, and artificial intelligence to predict and prevent security incidents before they occur, identify hidden risks, and provide real-time information to prevent failures and reduce the possibility of accidents.
Studies and research support this approach such as Deloitte’s “Pioneering Safety in the Fourth Industrial Revolution” which explores the use of technology to improve safety in the workplace, and the article “Predictive Safety Analytics: Progress, Opportunities, and Challenges,” published in Safety Science magazine, which presents the key advances and challenges of predictive safety.
Preventive occupational safety is a set of techniques, methods and practices for the prevention of accidents and occupational diseases in the work environment that aims to encompass the identification of risks and hazards present and the adoption of preventive measures to avoid or minimize these risks, applying technical and scientific knowledge. One of the methods used is Design for Safety (DFS), which seeks to integrate safety from the beginning of the design process of products, equipment, and installations, based on international norms and standards, such as ISO 12100 – Safety of Machinery, ANSI/ASSE Z590.3 – Prevention Through Design Guidelines, and NR12 – Regulatory Norm for Safety at Work in Machinery and Equipment.
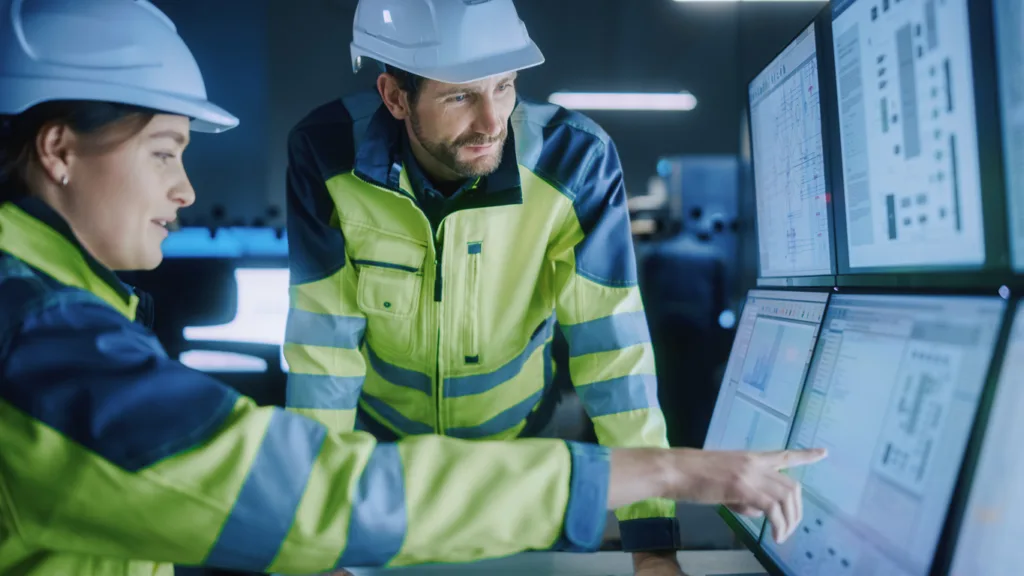
Safety 4.0 and its various applications.
Just like “Industry 4.0”, we should consider the concept of “Safety 4.0” as technology can be used to significantly improve health and safety. As a consequence of the fourth industrial revolution, such as the internet of things (IoT), artificial intelligence (AI), advanced robotics, and cloud computing, Safety 4.0 adopts these messy technologies to improve safety in the workplace.
The benefits include reduced risk of accidents and injuries, increased efficiency and productivity, improved occupational health and safety risk management, and enhancement of the safety culture in companies. There are already several initiatives and studies being carried out in this direction, such as the publication “Safety 4.0: A New Era in Industrial Safety” by the Institute of Electrical and Electronic Engineers (IEEE). Some examples:
- The use of fatigue and stress sensors to help detect fatigue or stress, alerting to take regular breaks, or health monitoring devices such as smart watches and motion sensors to monitor health and prevent injury and illness, and even mobile apps to provide real-time occupational safety and health information as well as allow workers to report hazards and accidents, such as those from Drixit.
- Virtual or Augmented Reality, used to train workers in hazardous conditions and simulate emergency situations increasing the effectiveness of training.
- Collaborative robots, which work together with workers, increasing the efficiency of the production process, or to perform repetitive or dangerous tasks in confined spaces.
- Data analysis and machine learning algorithms that help identify risk trends and patterns, predicting and preventing accidents and enabling more effective preventive measures to be taken.
- The use of drones to inspect equipment in hazardous areas and sensors to detect the presence of toxic gases.
- Chatbots to provide occupational health and safety information to workers, and facial recognition systems to detect the presence of unauthorized workers in hazardous areas.
Workplace safety: one of the broader dimensions of sustainability.
Contextualizing before the ESG (Environmental, Social and Governance) in the letter “S”, adopting adequate safety and health practices promotes a safe and healthy work environment, contributing to the improvement of the quality of life of workers and, consequently, of society in general, bringing economic and governance benefits to companies, reducing costs with accidents, improving productivity, and increasing employee satisfaction.
In the SDGs (Sustainable Development Goals) of the UN, safety at work is in goal 8.8, “protect labour rights and promote a safe and secure work environment for all”, in goal 3.4 (health and well-being), in goal 9.4 (industry, innovation, and infrastructure), and in goal 11.6 (sustainable cities and communities), thus being one of the broader dimensions of sustainability.
We can affirm that we are effectively living the fourth revolution for Safety and that workers, companies, prevention professionals, directors, and board members need to have these concepts highlighted in their current and future business decisions as a strategic point for corporate governance and the sustainable future of organizations.
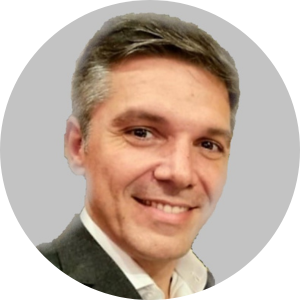
ABOUT THE AUTHOR
An HSE professional with a career spanning more than 30 years, Jeser Madureira has extensive experience in multinational companies, in management and leadership positions as a senior executive in ESG, Quality, HSE, Operations and People. In addition, he has a post-graduate degree in process engineering, an MBA and a master’s degree in HSE.