Las paradas de planta son momentos cruciales en la vida de una instalación industrial, donde se detiene temporalmente la producción para el mantenimiento, reparación y mejoras. Garantizar la seguridad en estos eventos, especialmente cuando se involucran contratistas externos, es esencial. En este artículo, exploraremos la importancia de gestionar adecuadamente la seguridad en las paradas de planta y las tecnologías que pueden contribuir a un entorno más seguro.
Qué es una parada de planta.
Una parada de planta se refiere al proceso en el que se detiene temporalmente toda o parte de la producción de una instalación industrial o fábrica, para llevar a cabo tareas de mantenimiento, reparación, inspección, ajustes o mejoras en el equipo, maquinaria, sistemas o instalaciones. Son paradas programadas y planificadas con antelación para minimizar interrupciones en la producción y garantizar un funcionamiento seguro y eficiente de la planta.
Las paradas de planta pueden variar en duración, desde unas pocas horas hasta varios días o incluso semanas, dependiendo de la naturaleza de las actividades que se necesitan realizar. Durante una parada de planta, el personal técnico y de mantenimiento realiza trabajos como la revisión y reparación de equipos, reemplazo de piezas desgastadas, inspección de tuberías y sistemas, actualización de software, y otros procedimientos necesarios para mantener la operación de la planta en óptimas condiciones. Además, estas paradas también son oportunidades para implementar mejoras tecnológicas y optimizar los procesos de producción.
Presencia de contratistas en paradas de plantas.
Las paradas de plantas suelen requerir de empresas externas especializadas en mantenimiento y técnica, que facilitan un número elevado de personal cualificado, herramientas y medios específicos para realizar las tareas necesarias. Los contratistas son aquellos trabajadores externos que participan en la parada de planta.
Los contratistas están habituados a trabajar en tareas técnicas y de mantenimiento, pero al no ser los trabajadores de planta permanente, no conocen los riesgos propios de la planta en cuestión. Uno de los principales desafíos de seguridad en las paradas de planta es la falta de conocimiento del lugar por parte de los contratistas, dado que son operaciones que se llevan a cabo normalmente en una misma planta cada 4 o 5 años, y el personal puede variar.
Además, de suceder un accidente grave, esto podría retrasar los tiempos previstos de la parada de planta, con un impacto económico directo al retrasar el inicio de la producción. De hecho, según un informe de la Asociación americana de Petroquímicos y Refinadores, el 80% de estas operaciones acaban superando en un 10% los costes previstos si no se realizan con la preparación y planificación necesaria.
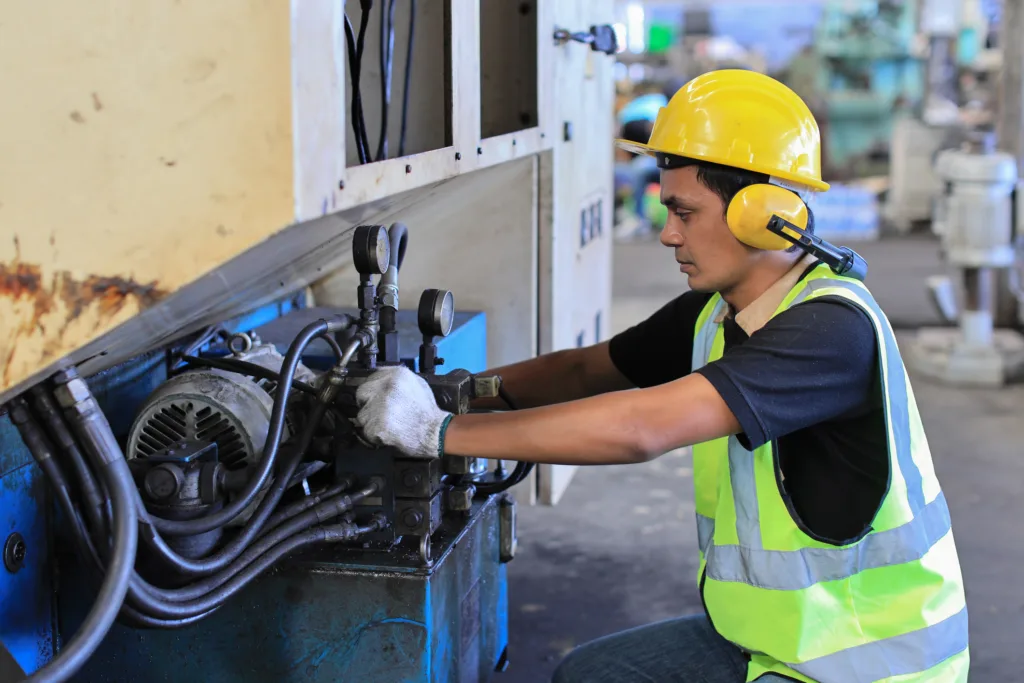
Peligros más habituales en paradas de planta.
Hay distintas razones que pueden llevar a diversos inconvenientes. Las más habituales son:
1# Falta de planificación: Intentar realizar un gran número de intervenciones en un corto período de tiempo, sin la debida organización previa. Para lograr reducir tiempos, la planificación y experiencia es clave.
2# Contratistas sin experiencia: Es de vital importancia seleccionar minuciosamente las empresas contratadas para realizar la parada de planta, asegurándose de que puedan proporcionar el personal calificado requerido.
3# Aumento de accidentes: La probabilidad de accidentes laborales aumenta significativamente con tanto personal externo y trabajo de mantenimiento, lo que conlleva tareas extras de los líderes de HSE para asegurar la protección de todos los trabajadores. Esto implica verificar las formaciones necesarias del personal que intervendrá, analizar los posibles riesgos que puedan surgir durante la ejecución de los trabajos, y evaluar el estado de los equipos y herramientas que se utilizarán.
Tecnología disponible para mayor seguridad.
Además de los ya habituales equipos de protección personal para trabajadores, para lograr una mayor seguridad en las paradas de planta pueden utilizarse diversas tecnologías y prácticas. Estas incluyen:
- Sistemas de Control y Automatización: La automatización de procesos y sistemas de control avanzados permite supervisar y controlar las operaciones durante la parada de planta de manera más eficiente y segura. Esto incluye la capacidad de detener y reiniciar equipos de manera precisa, monitorear variables críticas y realizar ajustes necesarios en tiempo real.
- Sistemas de Detección de Fallas y Alarmas: Se emplean sistemas de detección de fallas y alarmas tempranas que alertan al personal ante situaciones potencialmente peligrosas. Esto incluye la monitorización continua de sensores y dispositivos para detectar anomalías.
- Sistemas de Localización en Tiempo Real: Estos sistemas permiten rastrear la ubicación de trabajadores y equipos en tiempo real, lo que es especialmente útil para garantizar la seguridad y para coordinar las actividades durante la parada.
- Robótica y Drones: Los robots y drones pueden ser utilizados para inspeccionar áreas de difícil acceso o peligrosas sin exponer a los trabajadores a riesgos innecesarios.
- Gestión de Datos y Analítica: El análisis de datos en tiempo real y el almacenamiento de datos históricos pueden ayudar a identificar patrones y tendencias que pueden mejorar la seguridad y la eficiencia de las operaciones durante una parada de planta.
- EPP digitales: El uso de un EPP digital, tal como el Drixit Tag, provee una infinidad de soluciones pensadas especialmente para el trabajador industrial: botón de pánico, detección de entrada y permanencia en áreas de riesgo, detección de trabajo en altura, localización precisa en caso de emergencia y evacuación, entre otras. Su incorporación permite prevenir y mitigar accidentes industriales, asegurando una correcta parada de planta y evitando posibles demoras.
La combinación de estas tecnologías, junto con la capacitación adecuada y una sólida cultura de seguridad, contribuye a lograr una mayor seguridad en las paradas de planta, minimizando los riesgos para los trabajadores y garantizando un retorno eficiente a la operación normal.