As paradas de planta são momentos cruciais na vida de uma instalação industrial, em que a produção é temporariamente interrompida para manutenção, reparos e atualizações. É essencial garantir a segurança nesses eventos, especialmente quando há empreiteiros externos envolvidos. Neste artigo, exploraremos a importância de gerenciar adequadamente a segurança durante as paradas da planta e as tecnologias que podem contribuir para um ambiente mais seguro.
O que é uma paradas de planta ?
Uma paradas de planta refere-se ao processo no qual toda ou parte da produção em uma instalação industrial ou fábrica é temporariamente interrompida para realizar tarefas de manutenção, reparos, inspeções, ajustes ou melhorias em equipamentos, máquinas, sistemas ou instalações. Essas paralisações são programadas e planejadas com antecedência para minimizar interrupções na produção e garantir um funcionamento seguro e eficiente da planta.
As paradas de planta podem variar em duração, indo desde algumas horas até vários dias ou mesmo semanas, dependendo da natureza das atividades que precisam ser realizadas. Durante uma paradas de fábrica, pessoal técnico e de manutenção realiza tarefas como inspeção e reparo de equipamentos, substituição de peças desgastadas, inspeções de tubulações e sistemas, atualizações de software e outros procedimentos necessários para manter a operação da planta em condições ideais. Além disso, essas paralisações também oferecem oportunidades para implementar melhorias tecnológicas e otimizar os processos de produção.
A presença de contratantes em paradas de planta .
As paradas de planta frequentemente exigem empresas externas especializadas em manutenção e técnica, que fornecem um grande número de pessoal qualificado, ferramentas e meios específicos para realizar as tarefas necessárias. Contratantes são trabalhadores externos que participam da paradas de planta .
Os contratantes estão acostumados a trabalhar em tarefas técnicas e de manutenção, mas, por não serem trabalhadores permanentes da planta, podem não estar familiarizados com os riscos específicos da planta em questão. Um dos principais desafios de segurança durante as paradas de planta é a falta de familiaridade dos contratantes com o local, já que essas operações geralmente ocorrem na mesma planta a cada 4 ou 5 anos, e o pessoal pode variar.
Além disso, um acidente grave pode resultar em atrasos na paralisação planejada, causando impactos econômicos diretos ao adiar o reinício da produção. De fato, de acordo com um relatório da Associação Americana de Petróleo e Refino, 80% dessas operações acabam excedendo os custos projetados se não forem adequadamente preparadas e planejadas.
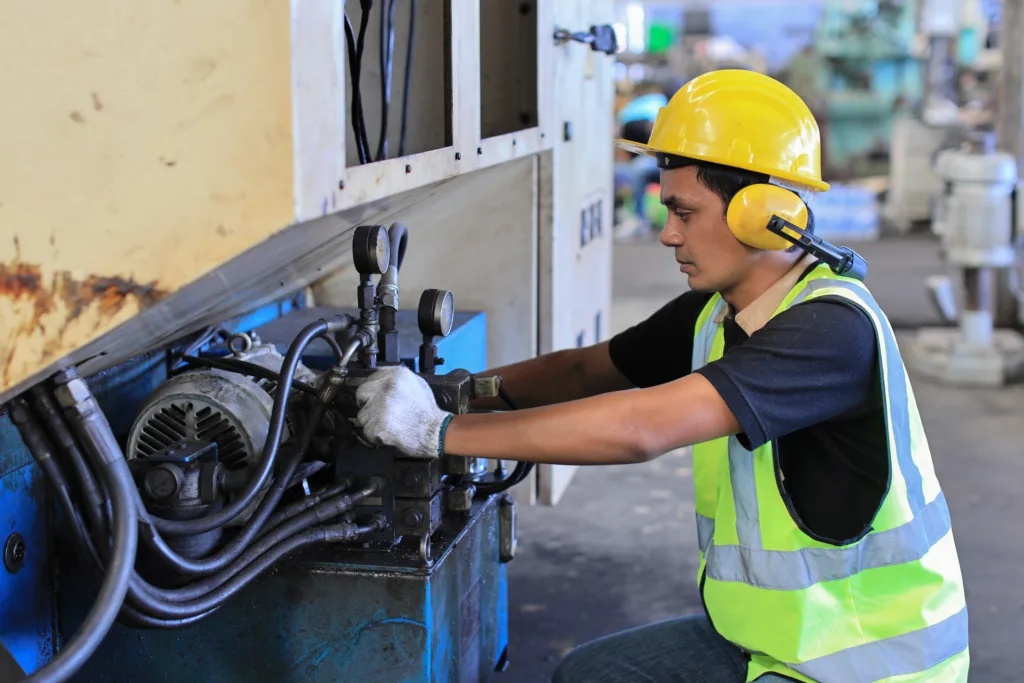
Perigos comuns em paradas de planta .
Vários fatores podem levar a diversos problemas, sendo os mais comuns:
1# Falta de Planejamento: Tentar realizar um grande número de intervenções em um curto período de tempo sem a devida organização prévia. O planejamento eficaz e a experiência são fundamentais para reduzir o tempo de inatividade.
2# Contratantes Inexperientes: É vital selecionar cuidadosamente as empresas contratadas para a paradas de fábrica, garantindo que possam fornecer o pessoal qualificado necessário.
3# Aumento de Acidentes: A probabilidade de acidentes de trabalho aumenta significativamente com a presença de pessoal externo e trabalho de manutenção, exigindo esforços adicionais dos líderes de HSE para garantir a proteção de todos os trabalhadores. Isso envolve verificar o treinamento necessário para o pessoal envolvido, analisar os riscos potenciais durante a execução do trabalho e avaliar o estado dos equipamentos e ferramentas a serem usados.
Tecnologia disponível para aumentar a segurança.
Além do equipamento de proteção pessoal padrão para os trabalhadores, várias tecnologias e práticas podem ser usadas para aumentar a segurança em paradas de planta. Estas incluem:
- Sistemas de Controle e Automação: A automação de processos e sistemas de controle avançados permite monitorar e controlar as operações durante a paradas de planta de forma mais eficiente e segura. Isso inclui a capacidade de parar e reiniciar equipamentos de forma precisa, monitorar variáveis críticas e fazer ajustes em tempo real.
- Sistemas de Detecção de Falhas e Alarmes: São usados sistemas de detecção de falhas e alarmes que alertam o pessoal para situações potencialmente perigosas. Isso envolve a monitorização contínua de sensores e dispositivos para detectar anomalias.
- Sistemas de Localização em Tempo Real: Esses sistemas permitem o rastreamento em tempo real de trabalhadores e equipamentos, sendo especialmente úteis para garantir a segurança e coordenar atividades durante a paralisação.
- Robótica e Drones: Robôs e drones podem ser usados para inspecionar áreas de difícil acesso ou perigosas sem expor os trabalhadores a riscos desnecessários.
- Gestão de Dados e Análises: A análise de dados em tempo real e o armazenamento de dados históricos podem ajudar a identificar padrões e tendências que podem melhorar a segurança e a eficiência operacional durante uma parada de planta.
- EPI Digital: A utilização de equipamento de proteção pessoal digital, como a Tag Drixit, oferece uma ampla gama de soluções projetadas especificamente para trabalhadores industriais, incluindo botões de pânico, detecção de entrada e permanência em áreas de risco, detecção de trabalho em altura, localização precisa em caso de emergência e evacuação, entre outras. Sua implementação ajuda a prevenir e mitigar acidentes industriais, garantindo uma bem-sucedida parada de planta e evitando possíveis atrasos.
A combinação dessas tecnologias, juntamente com o treinamento adequado e uma sólida cultura de segurança, contribui para alcançar uma maior segurança em paradas de planta , minimizando os riscos para os trabalhadores e garantindo um retorno eficiente à operação normal.